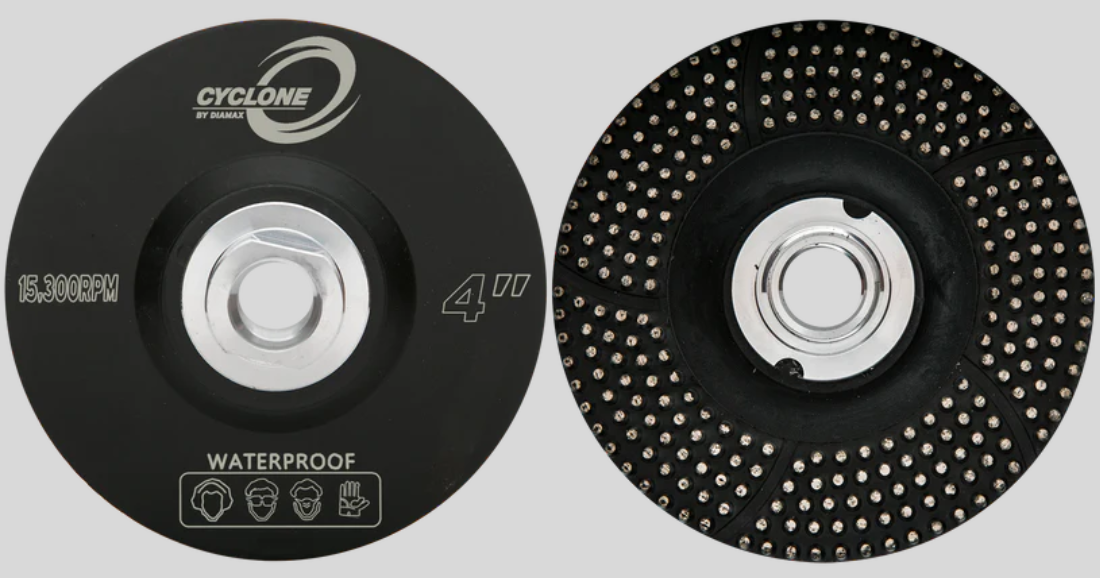
Comparing Floor Polisher Methods: Wet vs. Dry Grinding and Polishing Unveiled
Share
Are you looking for the best method to grind and polish your floors? But are you confused about which one to choose? This blog will answer you! There are two primary methods from which you can choose: wet and dry grinding and polishing. Both methods have pros and cons; choosing the right one for your needs can significantly affect the final results. This blog will explore the differences between wet and dry grinding and polishing methods and help you determine which is best suited for your floor. You will get to know how each of them works and what their pros and cons are. We will also share some major maintenance and care tips for you to understand and make a great choice! So, keep on reading this!
What are Concrete Grinding Wheels, and How Do They Work?
Concrete grinding wheels are tools used in construction to smooth and polish concrete surfaces. They work like sandpaper but are much stronger. These wheels have abrasive particles, like tiny rough bits, embedded in them. When you attach the wheel to a grinder, it spins, and those abrasive particles do the hard work of grinding down the rough spots on the concrete.
Here's how it works:
- Smoothing Out Roughness: When concrete is poured, it can have bumps, rough areas, or uneven spots. Grinding wheels help by smoothing these out, making surfaces even and safer.
- Removing Imperfections: Sometimes, concrete surfaces have imperfections or old coatings. Grinding wheels take them off, revealing a clean, fresh layer of concrete.
- Polishing for a Shine: If you want a polished, glossy finish, these wheels can achieve that, too. They gradually refine the surface, giving it a professional look.
- Types of Grinding Wheels: There are different grinding wheels for various tasks. Some are for heavy-duty grinding, while others are for polishing. Choosing the right one depends on the job you're doing.
What Is Dry Grinding?
Dry grinding is a material removal process that is widely used in many industries to produce smooth and flat surfaces on a variety of materials. Unlike wet grinding, dry grinding does not require the use of a liquid coolant. Instead, it uses abrasives to remove material from the workpiece. Dry grinding offers several benefits, including cost-effectiveness and portability, but it also comes with some potential drawbacks, such as heat generation and the creation of dust and airborne particles.
Pros
1. Cost-Effective Method
Dry grinding is a cost-effective method of material removal. Because it does not require the use of a liquid coolant, it is less expensive than wet grinding, which requires the purchase and disposal of coolant. In addition, the process requires less energy, making it more energy-efficient and cost-effective.
2. Portability and Convenience
Dry grinding is a more portable and convenient method of material removal than wet grinding. Because it does not require access to a water source or drainage system, it can be used in a variety of settings, including remote locations or areas with limited water resources. In addition, it is a more convenient process because it does not require the use of a liquid coolant, which can be messy and difficult to manage.
Cons
1. Heat Generation and Potential Damage
One of the main concerns with dry grinding is the generation of heat during the grinding process. This heat can cause damage to the workpiece, particularly if it is made of a material that is sensitive to heat, such as plastic or certain types of metal. In addition, the heat can cause the workpiece to deform or warp, which can affect its accuracy or quality.
2. Dust and Airborne Particles
Another potential drawback of dry grinding is the creation of dust and airborne particles during the grinding process. These particles can harm workers' health and safety if they are not properly protected. In addition, they can cause damage to machinery or other equipment if they are not properly contained or removed.
Dry grinding is a popular method of material removal in many industries due to its cost-effectiveness and convenience. However, it comes with some potential drawbacks, such as heat generation and the creation of dust and airborne particles. With proper precautions and safety measures, dry grinding can be a safe and efficient way to produce high-quality surfaces on a variety of materials.
What is Wet Grinding
Wet grinding is a method of material removal that involves the use of a liquid coolant, typically water, to cool and lubricate the grinding process. This process is commonly used in manufacturing to produce smooth and precise surfaces on metal, wood, and other materials.
Pros
1. Dust Suppression
Wet grinding provides dust suppression during the grinding process, which can be important for worker safety and environmental regulations. Using a liquid coolant helps control the dust and debris produced during grinding, which can help prevent respiratory issues and keep the workspace clean.
2. Cooling and Lubrication
The liquid coolant used in wet grinding provides cooling and lubrication to the grinding process, which can help to prevent damage to the workpiece and the grinding tool. The coolant helps to dissipate heat generated during the grinding process, which can reduce the risk of damage to the workpiece and improve the quality of the finished product.
Cons
1. Mess and Cleanup
One of the main concerns with wet grinding is the mess and cleanup involved in the process. Using a liquid coolant can result in spilled coolant and debris, which can be difficult and time-consuming to clean up. Additionally, using a liquid coolant can increase maintenance and cleaning requirements for the grinding equipment.
2. Increased Operational Cost
Using a liquid coolant in wet grinding can result in increased operational costs, as the coolant must be purchased, stored, and properly disposed of after use. Additionally, the use of a liquid coolant can result in increased electricity usage for pumps and other equipment needed to circulate the coolant.
Wet grinding is a popular method of material removal in many industries due to its ability to provide dust suppression, cooling and lubrication during the grinding process. However, it comes with some potential drawbacks, such as mess and cleanup and increased operational costs. With proper precautions and safety measures, wet grinding can be a safe and efficient way to produce high-quality surfaces on a variety of materials.
Maintenance and Care of Concrete Grinding Wheels
Concrete grinding wheels are essential to grind and smooth concrete surfaces. These wheels are made of abrasive materials that can wear down over time due to constant use and exposure to various elements. Proper maintenance and care are crucial to ensure that these wheels remain effective in producing smooth and even surfaces.
Here are some tips for maintaining and caring for your concrete grinding wheels:
- Keep the Grinding Wheels Clean:
Keeping the grinding wheels clean is essential to ensure they operate effectively. Dirt, debris, and other contaminants can reduce the wheels' effectiveness, causing them to wear out sooner. To keep the grinding wheels clean, use a soft brush to remove any accumulated debris or dirt on the wheels.
- Check for Damage:
Inspect the grinding wheels for any signs of damage, such as cracks or chips. These defects can reduce the effectiveness of the wheels and cause them to break during use, posing a safety hazard. If any damage is detected, replace the wheels immediately.
- Store Appropriately:
Proper storage is crucial to maintaining the quality and effectiveness of the grinding wheels. Store the wheels in a cool, dry place, away from any moisture or humidity that can cause corrosion or other damage. Avoid stacking the wheels directly on top of each other, as this can cause them to deform or become misshapen.
- Use the Right Grinding Wheel for the Job:
Using the wrong grinding wheel for a particular job can cause the wheel to wear out quickly or become damaged. Always use the right grinding wheel type for the specific task. Consider the ground material, grinding speed, and desired finish.
- Use Proper Techniques:
Proper techniques when using the grinding wheels can help prolong their lifespan. Avoid applying too much pressure on the wheels, which can cause them to wear out more quickly. Additionally, avoid overheating the wheels during use, as this can reduce their effectiveness and cause them to wear out more quickly.
To Sum Up
As you have understood wet and dry grinding and how to maintain them for high durability, you can now decide which one is good for you and what kind of grinding method you can use for any specific project. But the major question is, where can you get the grinding wheels?
So, if you are looking for wet and dry grinding solutions, Tait Sales & Consulting offers a wide range of equipment and services to meet your needs. Our team of experts can help you select the best equipment for your specific application and provide ongoing support and maintenance to keep your equipment running smoothly.
In addition, Tait Sales and Consulting offers a variety of other services, including fabrication, welding, and machining, to meet all of your industrial needs. Are you in need of wet and dry grinding solutions for your business? Contact Tait Sales & Consulting to learn more and get started.