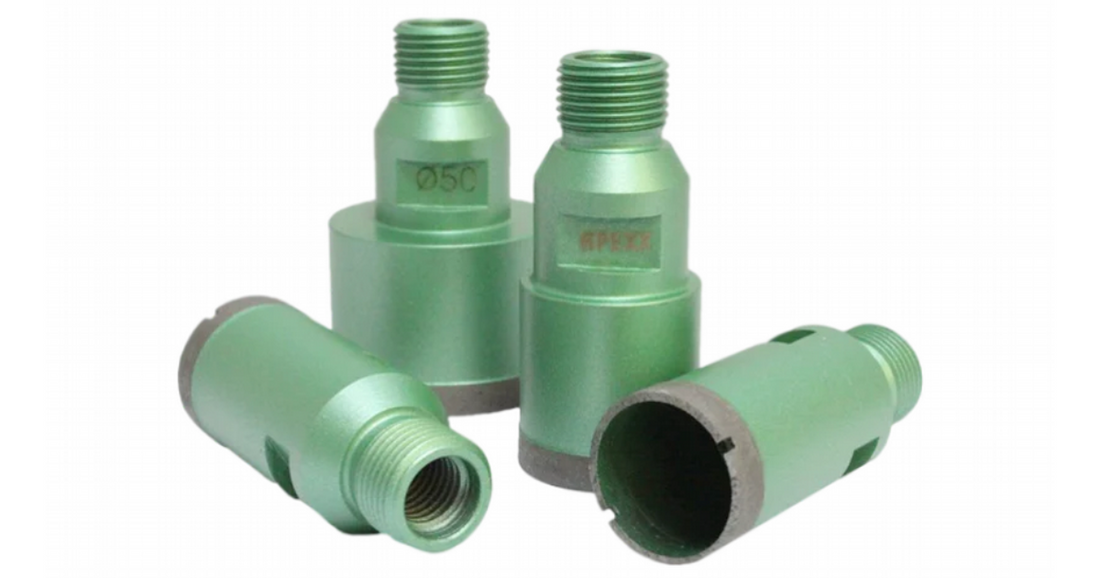
Stone-Cutting with High-Performance CNC Tooling: What You Need to Know
Share
CNC (Computer Numerical Control) tooling involves using specialized tools and equipment to cut and shape stone materials with high precision and efficiency. CNC machines are used in various industries, including architecture, construction, and manufacturing, to produce a wide range of stone products, such as countertops, tiles, monuments, and sculptures.
Understanding Stone Cutting CNC Machines
CNC machines involve several key components to achieve precise and efficient stone cutting. These key components include:
- Cutting tools: Cutting tools are one of the most important components of CNC tooling for stone cutting. These tools are typically made of diamond, the hardest material on Earth, and can precisely cut through stone. Diamond tools are available in various shapes and sizes, including flat, cup-shaped, and cylindrical, and are used for grinding, polishing, and cutting stone surfaces.
- CNC machines: CNC machines use cutting and shaping tools that grind precise and complex profiles on the stone edge. These machines have various cutting tools, including diamond tools, and can perform high-speed and high-precision cuts. CNC machines for stone cutting come in various types, including bridge saws, waterjets, and routers.
- Water filtration systems: Water filtration systems are used in CNC machines for stone cutting to prevent the buildup of debris and dust during the cutting and shaping process. Water is used as a lubricant and coolant to keep the diamond tools cool and reduce friction, which can cause damage to the stone and the tools.
- CAD/CAM software: CAD/CAM (Computer-Aided Design/Computer-Aided Manufacturing) software designs and programs the CNC machine to execute specific cutting and shaping operations. The software allows for precise control of the cutting tools and can be used to create complex 3D designs.
- Workholding devices: Workholding devices are used to secure the stone material in place during the cutting and shaping process. These devices come in various shapes and sizes, including clamps, vacuum pods, and jigs, and are designed to hold the stone material securely to prevent movement and ensure accurate cuts.
Overall, the key components of CNC tooling for stone cutting work together to produce high-quality stone products with precision and efficiency. It requires skilled operators familiar with the machinery and software and can produce high-quality stone products.
What Materials and Coatings Are Used for CNC Tooling?
CNC tooling encompasses a wide range of tools and accessories, including cutting tools such as drills, end mills, reamers, tool holders, calibration wheels, vacuum pods, and other fixtures that hold the workpiece in place during machining.
CNC tooling is essential to the CNC machining process as it determines the quality and accuracy of the finished part. The selection of appropriate CNC tooling depends on the machining operation's specific requirements, including the type of material being machined, the geometry of the part, and the desired surface finish. CNC tooling is available in various materials, such as carbide, high-speed steel, and ceramic, and can be customized to meet the specific needs of the machining operation.
The choice of materials and coatings used for CNC tooling depends on the type of application and the material being cut. Here are some commonly used materials and coatings for CNC tooling:
- Electroplating or Vacuum Brazed: Electroplated or Vacuum Brazing are two different processes for CNC tooling, that adheres the diamond directly to a solid steel core that does not lose shape as it grinds the profile into the stone. This is advantageous for complicated profiles. While the process differs in manufacturing, the end result tools behave comparably. The life of this tool is shorter than a sintered tool but has much less maintenance. These tools generally grind faster, have a much smaller labor cost, and virtually no maintenance.
- Sintered Continuous Rim Diamond: The sintered process for CNC Tooling will add a depth of diamond to a steel core for grinding profiles on stone. The advantage of this is an extended tool life. The disadvantage is that the profile loses shape as the tool wears. Ultimately, the tool must be returned to the manufacturer to have the profile ground back into the wheel. This process can usually be done 1 or 2 times in the CNC tools life. A lot of weekly maintenance must be performed to keep the tool at optimum performance. Because of this, the sintered tools are more labor-intensive.
- Sintered Segmented Diamond: The CNC Tooling that is most aggressive and for that do the first steps of creating a profile are the segmented wheels. These tools do most of the work, are very low grit, and lose shape and life the quickest. It’s important to change these first steps frequently as a worn position 1 segmented CNC tool will lead to damage on the wheel that follows.
How are Industries Leveraging CNC Tooling?
The stone fabrication industry has revolutionized how it works by introducing CNC tooling. CNC machines have provided a faster, more efficient, and more precise way of cutting and shaping stone materials. CNC tooling has enabled fabricators to easily create complex designs and shapes, providing greater design flexibility to customers. Automated production has also reduced the need for manual labor, resulting in improved productivity and efficiency. CNC machines have also enabled faster production times, reducing lead times for stone products. Additionally, the accuracy and consistency of cuts have improved the quality of finished products, reducing the chances of defects or mistakes. Overall, CNC tooling has helped the stone fabrication industry enhance the quality of stone products, increase efficiency and productivity, and offer greater design flexibility to customers.
Choosing the Right CNC Tools for Your Stone Cutting Needs
Choosing the right CNC tooling for your stone-cutting needs is crucial to achieving high-quality results, minimizing waste, and optimizing efficiency. Here are some factors to consider when selecting CNC tooling for stone cutting:
- Material type: The stone material being cut will determine the tooling required. Harder materials, such as granite and marble, will require the diamond tooling to have softer segments and rims (the bond), while softer materials, such as limestone and sandstone, will require a harder bond to last longer in the softer, more abrasive material.
- Tooling shape: The shape of the tooling will depend on the desired cut or shape of the stone material. Straight bits are ideal for straight cuts, while bullnose bits are better for curved cuts and complex shapes.
- Tooling size: The size of the tooling will depend on the thickness of the stone material being cut. Smaller tools are ideal for thinner materials, while larger tools are better suited for thicker materials.
- RPM Range: The recommended RPM range for the tooling will depend on the diameter and material of the tool. It is important to ensure that the RPM range of the tooling is compatible with the CNC machine being used.
- Machine Compatibility: It is important to ensure that the CNC tooling selected is compatible with the CNC machine being used. This includes ensuring the shank diameter and length are compatible with the machine's tool holder.
The Best Methods of Maintaining CNC Tooling
Several best practices can help you maintain tooling for CNC machines, including:
- Proper Storage: Store your tooling in a clean, dry, and temperature-controlled environment. Keep them in their original packaging or containers to protect them from damage.
- Regular Cleaning: Clean your tooling regularly to remove any debris or contaminants that can cause damage. Use a soft brush or compressed air to remove any chips or debris from the tooling. Avoid using harsh chemicals that can damage the coating or surface finish of the tooling.
- Inspection: Regularly inspect your tooling for signs of wear, damage, or other defects. Check for chips, cracks, or other damage to the cutting edge, and replace any tooling that shows signs of wear or damage.
- Calibration: Calibrate your tooling regularly to ensure accuracy and precision. Use a precision measuring instrument to check the dimensions of your tooling and make any necessary adjustments.
- Proper Handling: Handle your tooling with care to avoid damage or contamination. Avoid dropping, banging, or mishandling the tooling, and use proper lifting and handling equipment to move heavy or bulky tooling.
By following these best practices, you can ensure that your tooling for CNC machines remains in good condition and performs at its best. Regular maintenance can also extend the life of your tooling, reduce downtime, and improve overall productivity.